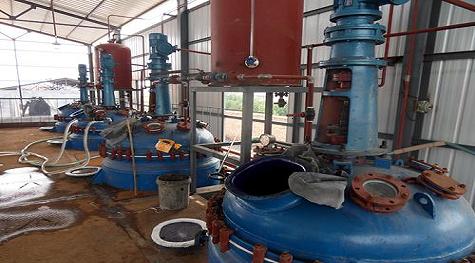
THE FIRST: SUMMARYGlass lined equipment belongs to the national one and second class pressure vessel, manufacturing, testing and acceptance strictly implement the national standard of HG2432-2001,widely used in the fields of petroleum, chemical industry, light industry, medicine, pesticide, dye and scientific research etc. Glass lined equipment is produced through special process, its glass lining surface is smooth and beautiful, have the advantages such as tensile strength, high corrosion resistance, heat resistance, easy to clean and do not pollute the material etc, but on the other hand the equipment have a vulnerability side, its price is higher and the glass lining is frangible, misusing may cause the enterprise or individual major economic loss, or even the life savety, so the user must be familiar with and master the relevant state of pressure vessel using range and the related regulations and the relevant knowledge of glass lined equipment etc, above are very important on increasing your benefit, to ensure your employees personal health, so the user before using must carefully read the this instruction for installation and using of our glass lined equipment, understand the basic knowledge of glass lined equipment, according to the instruction to installation and operation. THE SECOND: USER CHECKING 1.When the equipent reach the user, the relevant personnel of the user should check the equipment according to the supplier detailed delivering list such as the specifications, quantity, and the accessories specifications, quantity etc, if find some omitting feedback timely. 2.Check the equipment whether having collision and touch or not in transit to influence the quality, check the packaging loose or not. 3.The inspection of the Equipment for the user generally by looking the appearance to check the glass lining layer whether falling off or not; 4.When delivery the glass equipment, we don't do the electrical spark testing again, becase the eclectical spark test is a kind of destructive test which can influence the glass lining , but if the user still require it shall be indicated in the contract, wihich can do in our factory srictly according to the test method of HG2432-2001, otherwise please don’t do the test again, the retest voltage: 6KV.5.Open or close the manhole or another accessories should be lightly, don't allow impact the glass lining surface. When entering the vessel can't wear shoes with nails or sands, and should be laid the soft mat in bottom of the vessel.6.Tighten bolts and clips, the force should be equably, step-by-step, and should not tighten in one time , tighten not equably or over force will damage the glass lining and will not have good sealing effect.THE THIRD: HOISTING AND CARRYING1.The user should arrang the work with rich hoisting experience to do the hoisting and carrying work. 2. Before hoisting the sundry (wrench, hammer etc.) on the working stage must be taken away to avoid them falling into the vessel to damage the glass lining. 3.Before hoisting should confirm the hoisting equipment can stand the weight, should hoist ligtly to avoid the steel parts damage the glass lining. 4.When hoisting should lift by the equipment's ear in balance, forbiding by the nozzles of the equipment( the small capacity equipment can by the nozzle but should be carefully), in hoisting process should use the plastic soft mat to protect the glass lining to avoid impacting.5.For already installed well equipment, hoisting and carring should pay more attention, don't touch the mechanical seal and agitator. when carrying the large size equipment should use the wooden sticks to fix the agitator well .6.After hoisting, should check each of equipment parts becoming loose, falling off or not.THE FOURTH: INSTALLATING1.The already installed well equipment is simple, just hoisting the equipment and putting it inside the working stage which will be ok. 2.if need installation on the site, should place the agitator, cover, thermowell pocket etc glass lined parts on a rubber gasket to prevent damaging the glass lining, don't allow to put the glass lined parts on the hard ground directly. 3.Before installation, should confrim the vessel whether already adjusting in level or not, the equipment flange should be level with the datum, and the centerline of the central hole should be vertical with the datum. 4. When installating the agitator thermowell pocket, after opening the vessel cover, the soft mat should be laied in advance, then put into the agitator or thermowell pocket, to avoid droping down to impact and damage the glass lining of the vessel,agitator or thermowell pocket.. 5. After putting the agitator inside the vessel well, lifting the cover and close it well, then install the clips well. 6. For stuffing seal: Putting the stuffing box well on the agitation nozzle, the stuffing box should be concentric and level with the agitation nozzle and tighten the connecting bolts, 7.Put the reducer onto the the reducer supporting seat, adjust the adjusting nut to make the support seat, the agitator and stuffing box in one concentric.8. Put the agitator slowly passing the agitation nozzle, pay attention to avoid tocuhing the agitation nozzle, connect the agitator with the connecting shaft head of reducer well (connection mode have two kinds: thread-connecting and shaft coupling), again adjust the adjusting nut to make the support, the agitator and stuffing box in one concentric. 9. Put the packing material into stuffing box, pressing packing gland, if Installatting the mechanical seal, please see mechanical seal installation instructions. 10. For the drain valve, only when the spool and the installation orifice plate in one concentric then screw the bolts tightly, if eccentricity will make the valve can not be locked, 11. After the vessel and cover installed well with the agitator, then lifting and installating the reducer and the mechanical seal, 12.if equipment need to link with heavier pipes or towers, on the nozzle should install the fluorine compensator to relieve the stress, the nozzle can not be used as the pipe support, the external pipeline needing to add the supporting frame, 13. When installating pipes, the lateral of glass lined equipment shell forbidden welding accessories, all lnozzles should be sealed well to avoid something falling into the vessel to damage the glass lining.14. The fastening of the clips must be symmetry, i.e. tight in order and the forcibly is even, should not tight in one time, to avoid greatly forcibly in one local to damage the glass lining, for getting good sealing effect, it is better to put the steam inside the equipment slowly, when the gasket becoming soft then tight the clip next, when the lateral of gasket appearing drum shap the tigting is ok. 15. For electrical heating type equipment, the electrical heating bars must be completely submerged in the heating oil, must not dry heating, it is better to install a expansion tank to avoid the heated oil spilling.17. For steam heating equipment. must be installed a drain port, which should be installed in the higher nozzle of the equipment bottom. 18. Inlet steam pipe should be installed in the upper, cooling water pipe should be installed at the lowest nozzle of the equipment bottom. 19.The steam inlet valve should use the check valve.THE FIFTH: 221 TYPE DOUBLE MECHANICAL SEAL221 type double mechanical seal installation and debugging should be indicated in the purchasing contract , just as the total set is installed and tested well for delivery, generally for export equipments we have installed and tested the total set well for delivery, this construction is only a reference for the users can understand this kind of type double mechanical seal and can change it in future. The structure features: This kind of 221 type double mechanical seal is specially used for the Glass lined reactor, its main characteristic is standing higher pressure and strong corrosion resistance, the axial dimension is small, the structure is compact,the floatability of stationary seal is excellent, the installation requirements is not high. Due to seal face in seal chamber top, to avoid the impurities of sealant liquid and wear objects depositing around the the sealing surface, improved the sealinf condition, make the sealing effect is very reliable. This kind of seal is convenient installation and easy maintenance, and this kind of seal equiped the cooling water jacket usder by cooling to reduce the temperature to protect the sealing parts, which is helpful for improving its seal using conditions and the using life, the sealing liquid compressured by the nitrogen through the balance tank, and ensure the sealed pressure is higher than the vessel pressure about 0.5kg , in using only have little sealing liquid leaking and eliminate the harmful medium leaking, thus can eliminate the pollution in the chemical production process. 1.221 type double mechanical seal technical performance: (1)Standard name: seal series using for Glass lined reactor;(2)The code number: HG/T 2057-91; (3)Model: 221 type; (4)The working pressure: < 1.0 Mpa;(5)Application temperature: < 200 ℃;(6)Axle diameter: 30 ~ 130;(7)Rotational speed: below 300 RPM;(8)Suitable equipment: Glass lined reacotor.2, Use and maintain matters needing attention: (1)The mechanical seal's revelation quantity meeting to the stipulation of
is qualified (axle diameter ≥95mm:reveals quantity permission ≤10 ml/h;axle diameter ≤80mm, permission reveals quantity 8ml/h).(2)To connect the nitrogen cylinder through the reductor into the balance tank, adjusts the reductor, causes the pressure passing into the balance tank's higher than the largest working pressure 0.1 ~ 0.2 MPa inside the vessel.(3)In balance tank's oil(46no machine oil is ok) level should be in 2/3 position in its sight glass,when the oil level is excessively low should add the oil promptly.(4)In the working process should put the cycling cooling water inside the water jacket timely, the cycling water volume is good just as no leaking in the oil sealing position of the upper water jacket, the tap wateris ok, the connecting method: on its one side,the under nozzle input the cooling water,the upper nozzle output the cooling water,on another side, connecting those two nozzles with the U-type rubber pipe.(5)Periodic checking the oil level in the balance tank to judge the leaking situation of the mechanical seal, the oil level drops 1mm is about 12ml leaking(according to φ133x5 pipe calculating, other diameter's pipe, should recalculating), permission spillage 10ml/h.(6)After using for 3-6 months,should replace the sealing liquid, and flushes the sealed chamber, the balance tank and the cooling jacket, then adding the new sealing liquid.(7)Often raising the cooling water jacket to clean its arround feculence and the water scal.The sealing liquid use 46no machine oil or similar oil(if the medium inside vessel does not permit contacting machine oil, such as food,medicine etc, can use the cooking oil),to strictly filtrate the machine oil cleaning. 3.Installation and Disassembly: (1) Fix the water jacket and the mechanical seal main body on the agitation nozzle.(2) The mechanical seal stationary seal ring (porcelain ring) and the assembling bolt of the water jacket must tight for several times, may not tighten in one time, prevent the unevenly force to crush and damage the static ring.(3) The output shaft of reducer must be vertical and concentric to the mechanical seal stationary ring.(4) In order to put the wedge-shaped ring, the retainer, O-Ring of the cooling water jacket, the oil seal and the adjusting nut.(5) Install the reducer and its support on the vessel cover,tighten the nut of setting bolt.(6) From the lower extremity to put the agitator shaft through the intermediate bearing, twist the round nut and the lock gasket, turns the fingernail into the neighbor trough of the round nut,install the shaft coupling well.(7)Put the split clamp inside, turn on the adjusing nut to press downly the split clamp, the retainer causes the wedge-shaped ring to be smooth, presses the rotor ring inside upto visible gap under the locator card . clamping the clamps, takes down the locator card, fix the cooling watrer jacket well, put the locator card well for future disassembling using.The rotor ring of the mechanical seal must cause the spring to stand stress, and has certain adjustment distance.(8)Fixe the balance tank on the support seat, joins the pipes between the sealing fluid input and output nozzles.(9) Connect the pipes between the nitrogen cylinder well, the reductor and the balance tank.(10) When the sealing liquid compression to the working pressure to check the connecting points leaking or not.(11) The disassemblying order is opposite with the installation order, must attention to decompressing at first and let out the oil in the sealed chamber, fixed locator card well then can disassemblying.Note: The packing seal, the single mechanical seal installation is simple, no longer gives the detail. THE SIXTH: COMMISSIONING1.The painting on equipment outer surface is only for antirust and beautifu, when using, the nozzles surrounding should be added the protective measures, check the gaskets regularly to avoid leaking out the corrossion material to corrode the outersurface steel to form the outside reversing corrosion, 2.Before commissioning, must adding the oil the reducer and mechanical seal, then can drive; 3.Before driving by hand to turn the reducer to make the agitator rotating and listen to check whether having different sound and jam phenomenon or not; 4.The reducer steering direction must as the marking on the name plate, msut not reversing, if find revering , should stop immediately and adjust electrical conneting line , otherwise it will make the agitator fall off to damage the equipment.5.During the operating process, check the whole equipment operating performance normal or not, such as the reducer, the temperature of mechanical seal etc, if find different sound should immediately stop the operation, checking and removing the faults then do the test running again. 6.Water Pressure test: after the installation of equipment completed, according to the process conditions, should do the water pressure test in advance, i.e. using the water instead of the materia, input the compresssed air, to check all sealing postions whether leaking or not, find leaking position should tightly fixing the bolts or clips up no leaking, if everywhere no leaking can put the equipment into formal production. THE SEVENTH: EQUIPMENT USE1.The equipment operating workers must be trained specially according to this construction at first then can go to work, the records of operation of equipment must be carefully,clear and real (including the equipment purchase date, date of installation, commissioning situation etc), 2.Aftere period of using the quipment, should check the bolts and clips whether fastening or not, avoiding after long time using the gasket are failure. The gasket of any sealing position failure and appear leaking, should replaced i new gasket mmediately, before replacing the surronding should be cleaned, prevent the around corrosive materials remained; 3.Avoiding corrosive materials leaking from various nozzles, otherwise it will corrode the equipment from the outside surface, which is very harmful to the equipment.4. If the corrosive materials leaking on to the equipment surface, should be timely cleaning and neutralization the material, 5.Don’t allow to put the massive or hard things inside the equipment, avoid hiting and damage the glass lining.6. The lubricant of the reducer and mechanical should be replaced periodically(the oil cup of the reducer and the balance tank of the mechanical seal)7.Regular inspection to the cooling system of the water jacket operating well or not. 8.In the production process, the heating or cooling to the equipment should be slowly, don’t allow sudden heating or cooling, the cooling shock is 110 degree celsius, and the thermal shock is 120 degree celsius. 9.During the prodction process, the temperature of mechancial seal should be less than 70 degree celsius, the water jacket should be working to cycle the cooling water to protect the seal.THE EIGHTH: EQUIPMENT MINTENANCE1.Regularly checking the equipment working situation;2.The lubricant(machine oil) of the mechanical seal and reducer should change regularly (according to the working environment to decide) ;3.The vessel glass lining surface and the jacket don’t not allowed fouling or slagging. 4.The glass lining surface should often clean by water flushing, when cleaing, the temperature of the flushing water should be less than 50 degree celsius comparing with the vessel’s temperature. 5.Often check all gaskets of the equipment, if finding breakage, should change in time. 6.Often checking the glass lining of the equipment, if find strange, promptly notify us the strange situation or worn position etc details, we can accord to the details to give you the effective remedy measures, should not continue to use before our suggestion to avoid the deeply damage. 7.When the equipment already damaged beyond repair cases, according to detailed situation we can decide to repair or adopt another method.8.If the equipment need to storage for long time, should loosen all bolts and clips, all exposed mechanical parts should daub butter to avoid rusting. THE NINTH: OTHERSThe particulars have not indicated, please contact us in time. The final interpretation right of this Instruction belongs to Zibo CNCHEM Equipment Co.,Ltd.